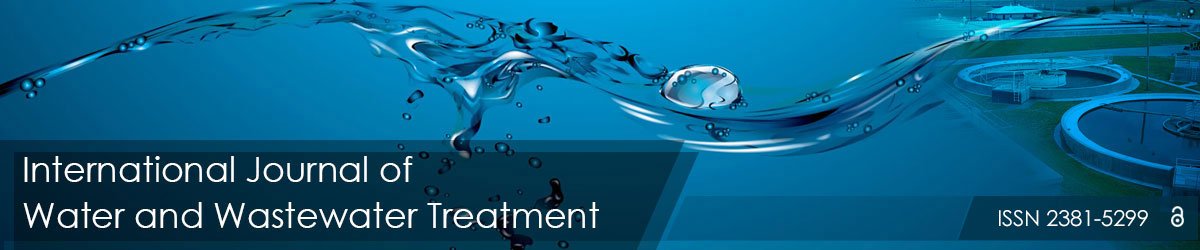
Full Text
Jessica M Higgs* Brenden R Bingham Rachel Boyer
Cache Environmental Laboratories, Layton, Utah, USA*Corresponding author: Jessica M Higgs, Cache Environmental Laboratories, 890 Heritage Park Blvd, Suite 202 Layton, Utah 84041, USA, Tel: 385-393-8841; E-mail: jessica@celcertifications.com
A preliminary study of the selective electrodeposition of Cadmium (Cd), Iron (Fe), and Chromium (Cr) from industrial wastewater sludge using alternating current. There are no large-scale methods for recovering the metals contained in the sludge resulting from industrial wastewater treatment. This study expanded on a method for using Alternating Current (AC) and a Graphene-Oxide-Modified Carbon Felt Electrode (CF-GO) by using a larger volume than previously used in literature and optimizing AC settings for the selected metals. Cd concentration in solution was reduced by 5-10% over five hours using an AC setting of 4 MHz, 2 Vpp, and -5 VOffset. Fe had five AC settings that had regression line slopes less than -4 ppm/ hr, and Cr had one AC setting with regression line slope less than -4 ppm/hr. As the Cr AC setting of 1 Hz, 1 Vpp, and -8 VOffset also was efficient for the electrodeposition of Fe, the Fe would need to be removed from solution before Cr. Future work outlined includes further AC optimization, additional metals also found in industrial wastewater sludge, optimization of the order of metals electrodeposited, and testing the method on industrial wastewater sludge.
Heavy metal; Electrochemistry; Industrial wastewater; Recycling; Reuse; Sludge
Global industrial processes can produce wastewater with high concentrations of heavy metals [1]. While treatment methods may be efficient, the current disposal protocol of metal-containing wastewaters presents hazards to the environment. Accumulation of heavy metals in living organisms in contaminated environments can contribute to various illnesses and diseases [2-5].
In most industrial processes, typical onsite treatment methods involve the removal of metals through precipitation [6]. The precipitated material, referred to as sludge, contains extraordinarily high levels of heavy metals and must be legally classified as hazardous waste. Current disposal methods of hazardous waste are limited and expensive, specifically the handling and shipping procedures. Additionally, flawed disposal procedures may lead to metals leaching into the environment [7].
Rather than bearing the cost to transfer and dispose of this hazardous waste, extracting the metals for recycling or salability purposes would be beneficial. For example, three wastewater treatment plants in South Africa treat approximately 3,500,000 liters per day collectively at an average cadmium influent of 0.11 mg/L [8]. With an average price of cadmium at $2.3/kg, approximately $323 of cadmium came through the plant in 2020. One method of extracting metal ions from solution is electrodeposition, which consists of applying an electric field across an electrochemical cell to produce oxidation-reduction reactions at the electrodes. This process allows metal ions to deposit on the electrode surface in their neutral state. Electrochemical methods have been employed in several applications, such as battery recycling [9], water desalination [10], and treatment of various industrial wastewaters [11-13]. While this method has proven to be efficient in reducing the concentration of metal ions in solution, it can be difficult to separate individual metals deposited due to coelectrodeposition or inhibition. Rögener F, et al. [14] noted that metals such as iron can inhibit the electrodeposition of other metals.
Recently, Liu C, et al. [15] researched a method to selectively electrodeposit lead, copper, and cadmium. Liu C, et al. [15] employed the use of Alternating Current (AC) sine waves and a grapheneoxide-modified carbon felt electrode (CF-GO) to selectively remove these metals. This CF-GO electrode was used to increase the active surface area and increase electrodeposition efficiency. Additionally, Liu C, et al. [15] determined optimum voltage, frequency, and offset values that would individually target their selected metals in solution. Conclusively, the method successfully obtained high recovery rates (>99.9%) and only minor losses (<1%) of other metal ions remaining in the solution.
This experiment investigated the removal of heavy metals by chemical electrodeposition for recovering that metal in its pure form and collectively reducing the chance of leaching into the environment. This study utilized and expanded Liu C, et al. [15] method to determine its use in removal of select heavy metals from industrial wastewater sludge for minimizing environmental leaching, reducing disposal costs, and possibly recycling for salability. Using the same method to prepare CF-GO electrodes, these experiments employed a larger electrochemical cell for the electrodeposition of a few of the metals found in industrial wastewater. Of the several metals expected to have relatively high concentrations in industrial wastewater, cadmium (Cd), chromium (Cr), and iron (Fe) were selected for this initial study. Cd was chosen to compare results with Liu C, et al. [15] Cr was chosen due to its high concentration and high monetary value, and Fe was selected due to its potential for inhibition of electrodeposition of other metals.
Graphene oxide modified carbon felt electrode preparation
The graphene oxide modified carbon felt electrode (CF-GO) was prepared similarly to the method used by Liu C, et al. [15]. A 2 mm thick carbon felt (CeraMaterials) was cut into 5 cm by 5 cm squares. The carbon felt to be modified was set as the negative electrode, and the positive electrode was either a strip of carbon felt (CeraMaterials) or a graphite rod (Graphite Store). Approximately 150 mL of 0.4wt% graphene oxide solution (MSE Supplies) was poured into a beaker and acidified it with 5 mL sulfuric acid for a pH ≈ 1. Next, 5VDC was applied to the electrodes for two hours using a function generator (RigolDG822). The modified carbon felt was then washed with DI water and air-dried.
Electrodeposition of heavy metals
The preparation of 1 L solutions of approximately 100 ppm of each of the metals of interest involved dissolving Cd(NO3)2, Fe(NO3)3, or Cr(NO3)3 (Sigma-Aldrich) in DI water. For the electrodeposition setup, the CF-GO was used as the working electrode and a carbon felt strip (CeraMaterials) or a graphite rod (Graphite Store) was used as the counter electrode, while a function generator (Rigol DG822) provided an AC signal.
For the electrodeposition of Cd, the AC signal was set to 4 MHz, 2 Vpp, and -5 VOffset. Two replicate experiments were recorded for this setting. AC signal settings for Cr and Fe electrodeposition were varied by offset, amplitude, and frequency. AC settings were selected to cover the maximum and minimum values of the range of interest (1 Hz to 10 MHz, 1 to 6 Vpp, 0 to -8 VOffset) within the voltage range of the function generator (total voltage range of -10 to 10 V). Additional AC settings were selected by computer-generated random values within the specified ranges for a total of 48 AC combinations as displayed in Supplementary table 1. Measurements of the metal concentration in the solutions were taken every hour. This procedure involved transferring an aliquot of approximately 10 mL of solution from the electrolytic cell, acidification with nitric acid, and filtration of the acidified sample portion into a 10 mL test tube to be analyzed by ICPOES. Readings were taken every hour for up to five hours to determine electrodeposition efficiency.
Combo # | Frequency | Amplitude (Vpp) | Offset (V) | Cr | Fe | ||
slope (ppm/hr) | R2 | slope (ppm/hr) | R2 | ||||
1* | 1 Hz | 1 | -8 | -4.68** | 0.933 | -6.09** | 0.934 |
-6.86** | 0.989 | -5.50** | 0.985 | ||||
2 | 10 MHz | 1 | -8 | -0.11 | 0.044 | -4.31** | 0.843 |
3 | 1 Hz | 2 | -8 | 0.38 | 0.148 | 1.12 | 0.392 |
4 | 10 MHz | 2 | -8 | -2.69 | 0.949 | 0.07 | 0.004 |
5 | 1 Hz | 1 | -6 | -1.41 | 0.655 | -0.13 | 0.013 |
6 | 10 MHz | 1 | -6 | -0.09 | 0.003 | -3.99 | 0.767 |
7 | 1 Hz | 4 | -6 | -0.42 | 0.463 | -3.21 | 0.587 |
8 | 10 MHz | 4 | -6 | -0.82 | 0.992 | -0.89 | 0.341 |
9 | 1 Hz | 1 | -4 | 0.16 | 0.028 | 1.40 | 0.834 |
10 | 10 MHz | 1 | -4 | -1.57 | 0.593 | 2.34 | 0.942 |
11 | 1 Hz | 6 | -4 | 1.48 | 0.765 | -1.51 | 0.908 |
12 | 10 MHz | 6 | -4 | 1.05 | 0.311 | 1.69 | 0.460 |
13 | 1 Hz | 1 | -2 | 0.80 | 0.228 | 1.21 | 0.273 |
14 | 10 MHz | 1 | -2 | 0.07 | 0.015 | -0.47 | 0.272 |
15 | 1 Hz | 6 | -2 | -0.62 | 0.704 | -2.24 | 0.774 |
16 | 10 MHz | 6 | -2 | -1.12 | 0.410 | -0.83 | 0.200 |
17* | 1 Hz | 1 | 0 | -0.60 | 0.359 | 3.37 | 0.377 |
-1.10 | 0.531 | -2.37 | 0.843 | ||||
18 | 10 MHz | 1 | 0 | -0.18 | 0.019 | -1.33 | 0.394 |
19 | 1 Hz | 6 | 0 | 0.07 | 0.003 | -0.91 | 0.303 |
20 | 10 MHz | 6 | 0 | 1.21 | 0.827 | -2.41 | 0.992 |
21 | 10 kHz | 6 | -4 | -0.72 | 0.355 | -0.14 | 0.039 |
22 | 10 Hz | 4 | -4 | -1.82 | 0.882 | -0.49 | 0.903 |
23 | 1 Hz | 4 | -2 | 0.75 | 0.793 | 3.15 | 0.863 |
24 | 100 Hz | 6 | 0 | 0.45 | 0.417 | 0.47 | 0.258 |
25 | 10 MHz | 4 | -4 | -1.66 | 0.474 | 0.92 | 0.712 |
26* | 100 Hz | 5 | -4 | -3.44 | 0.526 | -3.74 | 0.748 |
1.10 | 0.976 | -1.95 | 0.927 | ||||
27* | 100 kHz | 3 | -4 | -3.95 | 0.938 | -3.85 | 0.937 |
-3.95 | 0.834 | -5.50** | 1.000 | ||||
28 | 100 Hz | 1 | 0 | -3.59 | 0.977 | -2.69 | 0.815 |
29 | 10 kHz | 1 | -6 | -0.73 | 0.602 | -2.06 | 0.995 |
30 | 1 kHz | 5 | 0 | 0.59 | 0.155 | 1.33 | 0.607 |
31 | 1 kHz | 3 | -2 | -0.31 | 0.561 | -2.63 | 0.878 |
32 | 100 kHz | 2 | -6 | -2.79 | 0.872 | -3.03 | 0.809 |
33 | 100 Hz | 3 | 0 | -0.80 | 0.795 | -2.62 | 0.740 |
34 | 10 Hz | 2 | -6 | 0.43 | 0.067 | -5.01** | 0.945 |
35 | 10 kHz | 2 | -6 | 0.87 | 0.408 | -3.93 | 0.752 |
36 | 10 Hz | 4 | -2 | 1.36 | 0.378 | -0.06 | 0.002 |
37 | 1 MHz | 1 | -4 | -0.86 | 0.177 | -1.75 | 0.633 |
38 | 100 kHz | 1 | -6 | 1.20 | 0.678 | -1.47 | 0.787 |
39 | 1 Hz | 5 | 0 | 0.67 | 0.596 | 2.13 | 0.954 |
40 | 1 kHz | 3 | -4 | -1.24 | 0.814 | 0.49 | 0.085 |
41 | 100 kHz | 5 | -2 | 0.16 | 0.075 | -1.48 | 0.698 |
42 | 1 MHz | 6 | 0 | 0.15 | 0.029 | 0.41 | 0.106 |
43 | 10 Hz | 4 | -6 | -3.43 | 0.847 | 0.58 | 0.044 |
44 | 100 Hz | 1 | -2 | 0.00 | 0.000 | -0.09 | 0.034 |
45 | 10 MHz | 5 | -4 | -2.03 | 0.933 | -1.34 | 0.941 |
46 | 10 kHz | 3 | -2 | -0.20 | 0.014 | 0.23 | 0.021 |
47 | 1 kHz | 6 | 0 | -0.25 | 0.045 | 1.02 | 0.709 |
48 | 1 kHz | 5 | -4 | -0.15 | 0.031 | -0.64 | 0.243 |
Supplementary Table 1: AC signal combinations used for electrodeposition with the slopes and R2 values of the linear regressions of the loss of metal concentrations. Combinations indicated with an asterisk (*) had repeat experiments due to their higher electrodeposition efficacy. Slope values with a double asterisk (**) are less than -4 ppm/hr.
Electrodeposition of cadmium
One goal of this project was to reproduce the electrodeposition of Cd as performed by Liu C, et al. [15] using a larger volume of sample. At the AC settings of 4 MHz, 2Vpp, and -5 VOffset, there was a reduction of Cd concentration of 5-10% over 5 hours for the two samples analyzed (Figure 1). It is unclear presently why the measured concentration increased by about 4 ppm in the first hour of the experiment. One possibility is that the solution was not completely mixed at the time of the initial concentration reading, thus giving a lower-than-expected value. This can be remedied by using a stir plate in future experiments.
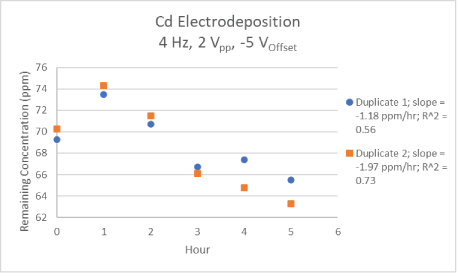
Figure 1: Reduction of cadmium concentration using the AC settings of 4 Hz, 2 Vpp, and -5 VOffset.
The original experiment by Liu C, et al. [15] used an AC range of (-5 V, -2 V) where this study used a range of (-6 V, -4 V) due to misinterpretation of the original paper. In Liu C, et al. [15] study, their settings essentially removed all the Cd from a 15 mL sample of 1000 ppm Cd solution within 8 hours with no decrease in electrodeposition efficiency over time. If time had permitted for the present study to use these settings, the solution of larger volume and lower concentration could take a longer than 8 hours to electrodeposit all the Cd.
Electrodeposition of chromium and iron
The second goal of this project was to determine if the AC settings could be optimized for the electrodeposition of Cr and Fe. After measuring the concentration of chromium and iron over time at the selected AC settings, a comparison of the linear fit slope was used to analyze the efficiency of electrodeposition (Supplementary table 1). Of the settings selected, the slope was less than -4 ppm/hr for one of the settings for Cr electrodeposition (1 Hz, 1 Vpp, -8 VOffset) and four of the settings for Fe electrodeposition(1 Hz, 1 Vpp, -8 VOffset, 10 MHz, 1 Vpp, -8 VOffset; 100 kHz, 3Vpp, -4VOffset; 10 Hz, 2 Vpp, -6 VOffset). Figure 2 shows the decrease in concentration over time for these settings. These are the most promising of our current results as shown with their steeper slopes.

Figure 2: Remaining metal concentrations over time for the electrodeposition of (a) chromium and (b) iron with linear regression slopes less than -4 ppm/hr. The AC setting of 1 Hz, 1 Vpp, -8 VOffset was duplicated for both chromium and iron. The AC setting of 100 kHz, 3 Vpp, -4 VOffset was one duplicate for the iron (Supplementary Table 1 for other duplicate value). Also, the data set for this setting is incomplete due to ICP issues and time constraints.
The most effective setting configuration tested for the electrodeposition of Cr (1 Hz, 1 Vpp, -8 VOffset) was also effective for the electrodeposition of Fe. This indicates that if this setting were chosen as the optimized AC signal for Cr electrodeposition, Fe would need to be removed from solution before Cr electrodeposition. With the results thus far, this could be possible with AC settings 10 MHz, 1 Vpp, -8 VOffset or 10 Hz, 2Vpp, -6 VOffset and running the experiment to completion. The setting of 100 kHz, 3 Vpp, -4 VOffset would not be as beneficial to use as there is some Cr electrodeposition at that setting as well (Supplementary table 1).
As the AC settings used in this study for the electrodeposition of Cd were not the same as those used by Liu C, et al. [15], it is expected that the adjustment of the AC voltage to 3 Vpp and -3.5 VOffset (maintaining the frequency at 4 MHz) would significantly improve the electrodeposition of Cd. To confirm this is the optimal AC setting, the AC components could be slightly adjusted to observe if electrodeposition efficiency increases or decreases. The efficiency can then be properly compared to that of Liu C, et al. [15] to determine if a larger sample volume affects the electrodeposition efficiency.
For the electrodeposition of Cr and Fe, there are many more AC settings that can be tested to optimize efficiency. This could be performed either by randomly selecting additional AC settings within the specified ranges, by testing AC settings slightly varied from the current most effective AC signals, and/or by implementing a software that can use a fraction factorial design of experiment to calculate optimized settings. With the optimized AC settings for Cd, Cr, and Fe, the order of electrodeposition can be determined by whether one metal can electrodeposit at the same settings as another metal. Most likely Fe will need to be removed from the solution first as seen with this experiment.
It will also be beneficial to determine optimized AC settings for other metals expected to be found in the prospective industrial wastewater sludge sample, such as nickel (Ni) and zinc (Zn), as these could possibly electrodeposit at the same AC settings as the other metals investigated. After optimizing the AC settings for the electrodeposition of the additional metals, these could then be factored into the order of electrodeposition based on their possibility of co-electrodeposition.
With the AC settings for the electrodeposition of each metal optimized and the order of electrodeposition determined, the proposed method could be used on a mixture of the metals and then on a sample of industrial wastewater sludge. The sludge may need either need acidification or a chemical digestion to dissolve the metal precipitate back in solution and decompose organic components used in the wastewater treatment process. If successful, this electrodeposition process can be up scaled to be implemented into current industrial wastewater treatment methods.
Some factors to consider when testing the proposed method at full-scale include increasing the size of the electrodes, testing that the AC settings for the selected metals are still optimized for the larger setup, using this process in-line as opposed to as a batch method, and extracting the deposited metals for recycling.
This study has confirmed that AC signal can be used in the electrodeposition of cadmium, chromium, and iron using graphene oxide modified carbon felt electrodes. Electrodeposition of cadmium reduced the concentration in solution by 5-10% over 5 hours, and it is expected that adjusting the AC settings to the optimized 4 MHz, 3Vpp, and -3.5 VOffset will increase electrodeposition efficiency to near complete extraction within eight hours. While more testing is needed for AC optimization of the electrodeposition of chromium and iron, the iron can likely be removed first at one AC setting (such as 10 Hz, 2 Vpp, -6 VOffset) followed by the chromium at a different AC setting (such as 1 Hz, 1 Vpp, -8 VOffset) based on the results of this experiment. This method could be used to recover valuable heavy metals from industrial wastewater sludge that can be sold and recycled while potentially reducing sludge volume and disposal costs.
- Fu F, Wang Q (2011) Removal of heavy metal ions from wastewaters: a review. J Environ Manage 92: 407-418. [Ref.]
- Luevano J, Damodaran C (2014) A review of molecular events of cadmium-induced carcinogenesis. J Environ Pathol Toxicol Oncol 33: 183-194. [Ref.]
- Costa M, Klein CB (2006) Toxicity and carcinogenicity of chromium compounds in humans. Crit Rev Toxicol 36: 155-163. [Ref.]
- Zambelli B, Uversky VN, Ciurli S (2016) Nickel impact on human health: An intrinsic disorder perspective. Biochim Biophys Acta 1864: 1714-1731. [Ref.]
- Plum LM, Rink L, Haase H (2010) The essential toxin: impact of zinc on human health. Int J Environ Res Public Health 7: 1342-1365. [Ref.]
- Gunatilake SK (2015) Methods of Removing Heavy Metals from Industiral Wastewater. J Multidiscip Eng Sci Stud 1: 12-18.
- Dutzik T, Crowell P, Rumpler J (2009) Wasting Our Waterways Toxic Industrial Pollution and the Unfulfilled Promise of the Clean Water Act. Environment America Research & Policy Center. [Ref.]
- Agoro MA, Adeniji AO, Adefisoye MA, Okoh OO (2020) Heavy Metals in Wastewater and Sewage Sludge from Selected Municipal Treatment Plants in Eastern Cape Province, South Africa. Water 12: 2746. [Ref.]
- Sze-yin T, Payne DJ, Hallett JP, Kelsall GH (2019) Developments in electrochemical processes for recycling lead–acid batteries. Curr Opin Electrochem 16: 83-89. [Ref.]
- Suresh A, Hill GT, Hoenig E, Liu C (2021) Electrochemically mediated deionization: a review. Mol Syst Des Eng 6: 25-51. [Ref.]
- Gupta B, Deep A, Tandon SN (2002) Recovery of Chromium and Nickel from Industrial Waste. Ind Eng Chem Res 41: 2948-2952. [Ref.]
- Oztekin Y, Yazicigil Z (2006) Recovery of metals from complexed solutions by electrodeposition. Desalination 190: 79-88. [Ref.]
- Tonini GA, Ruotolo LAM (2017) Heavy metal removal from simulated wastewater using electrochemical technology: optimization of copper electrodeposition in a membrane less fluidized bed electrode. Clean Techn Environ Policy 19: 403-415. [Ref.]
- Rögener F, Sartor M, Bán A, Buchloh D, Reichardt T (2012) Metal recovery from spent stainless steel pickling solutions. Resour Conserv Recy 60: 72-77. [Ref.]
- Liu C, Wu T, Hsu PC, Xie J, Zhao J, et al. (2019) Direct/Alternating Current Electrochemical Method for Removing and Recovering Heavy Metal from Water Using Graphene Oxide Electrode. ACS Nano 13: 6431-6437. [Ref.]
Download Provisional PDF Here
Article Type: SHORT COMMUNICATION
Citation: Higgs JM, Bingham BR, Boyer R (2022) Alternating Current for the Selective Electrodeposition of Cadmium, Iron, and Chromium Method Development for Simulated Industrial Wastewater Sludge. Int J Water Wastewater Treat 8(1): dx.doi.org/10.16966/2381-5299.182
Copyright: © 2022 Higgs JM, et al. This is an open-access article distributed under the terms of the Creative Commons Attribution License, which permits unrestricted use, distribution, and reproduction in any medium, provided the original author and source are credited.
Publication history:
SCI FORSCHEN JOURNALS
All Sci Forschen Journals are Open Access